How to choose the most suitable O-ring for your equipment?
How to choose the most suitable O-ring for your equipment? Engineers teach the secrets of selection
As a technical consultant who has been working in the seal industry for 12 years, I am often asked by customers: “Why does the O-ring I just replaced leak again?” Today I will use the actual case to tell you, choose the right O-ring material is actually like a car tire selection not only to see the parameters, but also to understand the actual working conditions.
First, from the workshop site to see the seal failure
Last week I went to visit an automobile parts factory, their hydraulic test bench frequent oil seepage problems. The scene to see the situation is very typical:
– The original nitrile rubber ring in 70 ℃ oil temperature began to harden
– The O-ring with a cross-section diameter of 5mm was flattened to 3.2mm (36% compression).
– Visible thermal cracks in the area close to the motor
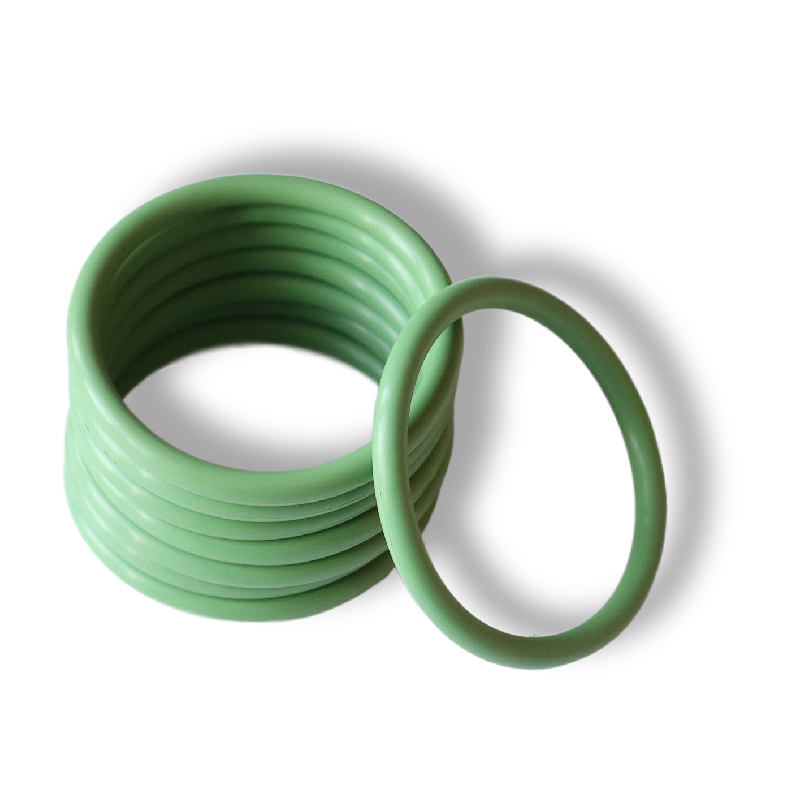
Nitrile rubber (NBR): It has excellent oil and fuel resistance and is commonly used in automobile, machinery and petrochemical industries. The disadvantage is that it is less resistant to high temperatures and is generally suitable for working environments from -30°C to 100°C.
“We chose the model exactly according to the manual!” The workshop director was full of confusion. In fact, the problem was the special needs of dynamic working conditions – they hadn’t taken into account the extra frictional heat caused by motor vibration.
Second, the three practical skills of material selection
1. temperature is not a single indicator
Remember handling a project in the North Sea oilfield in 2019? Although the wellhead temperature was only 80°C, the hydrogen sulfide environment made ordinary Viton brittle in 3 months. Later, we switched to DuPont’s Kalrez® 6375, which has a 6-fold improvement in corrosion resistance, although the nominal temperature resistance is only 275°C.
2. Chemical compatibility should be dynamically tested
Never just look at the material compatibility table! Last year’s medical device customer learned this lesson the hard way:
– Silicone rings in static tests are perfectly resistant to sterilizing liquids
– The ultrasonic vibration of the cleaning machine during actual use led to micro-cracks and accelerated chemical penetration.
– This led to micro-cracks and accelerated chemical penetration.
Now we always recommend our customers to do 200 hours dynamic simulation test. 3.
3. Compression rate needs to be carefully controlled
The “20% Golden Rule” shared by our friends in the automotive industry is not entirely accurate. In heavy duty hydraulic systems:
– Static seals: 18-22% compression is optimal.
– Rotary Seals: 12-15% is needed.
– Reciprocating: 8-10% recommended with Gattekamp retaining rings
Third, the industry veterans only know the alternatives
When standard solutions don’t work, try these proven workarounds:
1. Extreme Temperature Scenarios
– Low Temperature Challenge: Alaska Pipeline Uses Silicone Rubber Outsourced PTFE Film
– Hot and cold: German customer successfully applies graphite-filled EPDM to injection molding machine.
2. Response to special media
– Strong Acid Environment: Tokyo Chemical Plant Replaces Traditional FKM with Perfluoroether Rubber
– Food-grade requirements: Swiss chocolate equipment using platinum vulcanized silicone
3. Dynamic sealing optimization
– Hydraulic cylinders for agricultural machinery: polyurethane + molybdenum disulfide coating combination
– Automation equipment: HNBR with lubrication groove design
Fourth, to extend the life of the site maintenance skills
Recently helped the paper mill to do the transformation project is very illustrative: through three simple adjustments, O-ring replacement cycle from 3 months to 2 years.
1. Correct installation errors
– Reduce stretching by switching to a tapered installation tool
– Sprayed MoS2 dry film lubricant on groove surfaces.
– Strictly control bolt torque tolerance ±10 percent
2. Daily monitoring tools
– Monthly check of deterioration with portable hardness tester
– Infrared thermography to monitor abnormal friction hotspots
– Establishment of digital threshold for replacement warning
3. Failed parts analysis methods
– Failure mode is determined by slicing and observing the cross-section
– EDX elemental analysis to identify the source of contamination
– Measurement of permanent deformation by contour projector
V. 5 questions you must ask when purchasing
Based on my experience from the 143 supplier audits I’ve participated in, these key questions can prevent 90% of quality disputes:
1. “What is the range of hardness fluctuations between material lots?”
(Quality suppliers can achieve ±3 Shore A)
2. “Can you provide a vulcanization curve test report?”
(T90 time difference over 20% indicates process instability)
3. “What are the successful application cases under extreme working conditions?”
(Customer contact information is required for verification)
4. “Does the package contain ozone-proof barrier film?”
(Transportation and storage are often overlooked)
5. “Can the minimum order quantity support sample testing?”
(Be wary of vendors who unconditionally accept small purchases)
A Practical Toolkit for Engineers
– [Free Download] Dynamic Seal Calculation Template.xlsx
– [Online Test] Material Selection Decision Tree
– [Video Tutorial] 5 Common Installation Errors Demonstrated